Oil Water Separators: How They Work, Why They Matter, & How to Choose the Right One
- ameliya lanne
- Mar 17
- 6 min read
Updated: Jun 13
Have you ever wondered what happens to all that oily water produced in workshops, wash bays, or industrial sites? Are you curious about how businesses in Australia keep their processes clean and meet strict environmental regulations? If you are, you’re certainly not alone. Many organizations want to protect the environment while also saving on costs, and oil water separators (OWS systems) can play a massive role in making that happen.
In this blog post, we’ll dive into the world of oil and water separation. We’ll explore what oil water separators are, why they’re essential, and how they can benefit a wide range of industries. We’ll also look at the different types of separators—such as portable oil water separators, air compressor oil water separators, and specialised solutions—and discuss how to choose the right system.
By the end of this article, you’ll have a thorough understanding of oil water separators and a clearer picture of how they work. We’ll also talk about the top reasons to invest in one, plus best practices for keeping your system in top shape. Ready to learn more? Let’s get started!

What Are Oil Water Separators and Why Do They Matter
Oil water separators are systems designed to separate oil from water, allowing businesses to discharge or reuse the treated water more safely. This process is vital anywhere oil contamination is a concern, such as automotive workshops, construction sites, or marine environments. By preventing oil from entering water supplies or local ecosystems, an OWS system helps companies meet environmental regulations and maintain a responsible reputation.
Oil and water separation might sound simple, but it’s absolutely key for protecting both the environment and public health. When oil-contaminated water seeps into natural waterways, it can harm wildlife and plant life while also affecting local communities that rely on those resources. The costs associated with cleaning up contamination can be astronomical. That’s why installing an effective oil water separator is so critical—it reduces the likelihood of spills, pollution, and hefty fines.
How Oil Water Separators Work
Understanding the oil separator working principle helps you appreciate why these systems are so effective. In basic terms, oil floats because it’s less dense than water. An oil water separator capitalises on that difference, guiding oily water through various compartments or filters that allow oil to rise to the surface, where it can then be collected or skimmed off.
Most oil water separator systems are designed to slow down water flow, encouraging oil droplets to merge and rise. In a typical gravity-based unit, water moves through a chamber where small oil droplets collide and form larger droplets. Over time, these larger droplets gather on the surface. The separated oil is then directed into a holding tank, while the cleaner water is discharged or sent for further treatment. This principle underlies everything from a simple oily water cleaning device to more advanced systems designed for marine applications.
Key Components Explained
While all oil water separators share a core concept, they can vary in design. For instance, an air compressor oil water separator addresses the condensation formed when compressors cool compressed air. That condensation often carries traces of oil from the compressor’s internal lubricants. A compressor oil water separator collects and treats this mixture before safe disposal.
Similarly, a water separator compressor is another term used in industrial setups to describe a component that filters out moisture and oil from compressed air. These smaller, specialised systems—often referred to as air oil water separators—are crucial in factories or workshop environments. By removing oil before it circulates through other equipment, you preserve machinery and reduce maintenance costs.
Environmental Compliance and Regulations
Compliance with environmental regulations is a collaborative effort between businesses and government agencies. Installing an oil water separator is one of the most direct methods for meeting discharge standards, as it prevents harmful waste oil from contaminating waterways. This not only spares you from facing fines or legal troubles but also boosts your eco-conscious reputation. Clients and partners appreciate a business that shows commitment to reducing pollution—a clear win-win for your brand image.
Cost Savings and Operational Efficiency
Oil water separators might seem like a large expense at first glance. However, the long-term cost savings are often substantial. By treating oily water on-site, you reduce or even eliminate disposal fees for off-site treatment. Plus, you decrease wear and tear on pumps and other machinery because fewer contaminants circulate through your system. Over time, these savings can add up, making your operation more efficient and profitable.
Furthermore, the operational efficiency gained is hard to ignore. When your water is filtered correctly, you minimise clogs in drains and pipelines. You also cut down the possibility of emergency shutdowns due to built-up sludge. Those benefits translate directly into fewer maintenance hours and more productive days.
Safety and Workplace Hygiene
Oil spills or leaks create slippery surfaces that can be dangerous for employees. Even small drips around washing areas, air compressor setups, or industrial equipment can lead to accidents. Having an efficient oil water separator drain and a functioning OWS system helps keep surfaces clean and dry, lowering the risk of falls or injuries.
What’s more, properly managing oil-laden water stops foul odours and bacterial growth. Standing oily water can become a breeding ground for bacteria, which leads to unpleasant smells and potential health hazards. By removing oil promptly, your facility becomes a safer, healthier place to work.
Reduced Maintenance Demands
When oil isn’t effectively separated, it can rapidly gunk up equipment, lead to frequent breakdowns, and necessitate constant part replacements. Installing a well-designed oil water separator systems solution means less daily upkeep on pumps, pipes, and machinery. This is especially true in environments that use water separators for air compressors, as you avoid passing contaminated water vapor through your entire compressor network.
Taking care of an oil water separator technology system is also straightforward when you follow the recommended service intervals. You’ll spend fewer hours and resources dealing with emergencies and more time focused on core business activities.
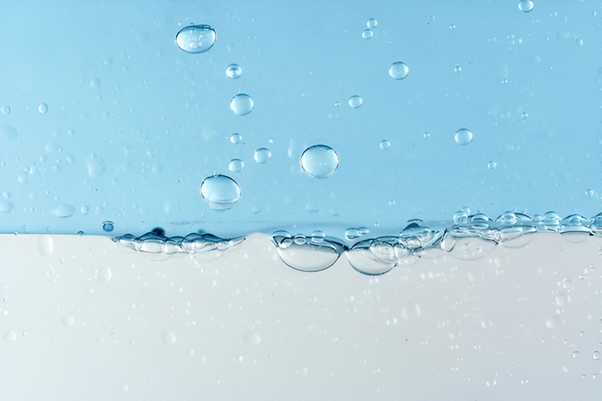
Choosing the Right Oil Water Separator
With so many models and types on the market, picking the right oil water separator can feel overwhelming. Yet by focusing on critical considerations like supplier reputation, local conditions, and specific system features, you’ll make a confident, well-informed choice. One of the easiest ways to ensure you’re getting a high-quality product is to consider well-known oil separators suppliers. A Cleanawater oil separator, for instance, is specifically built to meet Australian standards and handle local conditions. Do a quick check on each potential supplier’s track record, customer service policies, and system warranty. Testimonials from existing customers or industry peers can offer insight into how reliable that brand is in real-world conditions.
Weather intensity and local wastewater guidelines can vary widely across Australia. For example, areas with high rainfall might generate more runoff, requiring higher-capacity oil water separator systems. Meanwhile, if you’re dealing with extremely hot conditions, pick equipment designed to function well at higher temperatures. Be sure to check the manufacturer’s specs to confirm the unit can handle your site’s requirements—this includes flow rate capacity, discharge standards, and the type of contaminants involved.
Conclusion
To sum up, installing an oil water separator is a critical step for businesses producing oily wastewater. From automotive workshops and marine vessels to construction sites and industrial plants, these systems help you meet regulatory requirements while improving daily operations. They deliver peace of mind by safeguarding against pollution and fostering a safer work environment for your staff.
When you choose the right solution—be it a portable oil water separator or a fixed separator for your wash bay—you stand to gain cost savings, better efficiency, and a healthier workplace. Maintenance is straightforward once you learn how often to check and empty your system, and there are trusted oil separators suppliers ready to support you every step of the way.
Ultimately, investing in an oil water separator isn’t just about complying with rules. It’s about embracing a conscientious, forward-thinking approach to resource management. By taking control of your oily wastewater, you protect local ecosystems, promote workplace safety, and position your business as an environmental champion in the market. If you haven’t already, now is the perfect moment to move forward with a reliable oil water separator solution.
Comments